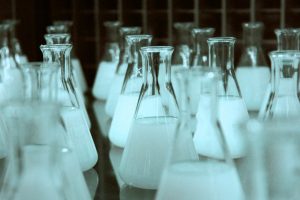
Sodium silicate is used in a wide range of industrial, construction, and environmental applications. Its characteristics allow it to be used as an adhesive, binder, accelerator for chemical reactions (such as in concrete), as well as a flame retardant, insecticide, acaricide, fungicide, or bleaching agent.
Soluble silicates are used as carriers to bind pigments and other powdered materials onto surfaces. As a surface coating, they increase surface resistance and form heat-resistant and intumescent films. Sodium silicate provides paints with a mattifying effect.
Typical applications
Functions of the silicate
Key benefits
Paints and Pigments
Chemical reaction.
Promotes dispersion. Provides a mattifying effect.
Sodium silicate has several properties that enhance its detergent qualities. It is an excellent emulsifying agent, as it promotes the reduction of the surface tension of liquids and improves the removal of dirt and stains. Furthermore, it keeps oily particles in suspension, preventing them from redepositing. The alkalinity of sodium silicates neutralizes acids, emulsifies fats and oils, and dissolves proteins. It maintains the desired pH even in acidic environments or solutions.
Typical applications
Functions of the silicate
Key benefits
Laundry Detergent Powder
Binder, corrosion inhibitor, deflocculant.
It helps the transformation of nebulized or agglomerated products. It protects against corrosion and cleanses.
Liquid detergents
Deflocculant, buffer.
Cleans, protects, and inhibits corrosion.
Silicate is widely used for bleaching cellulose, reducing the use of chlorine, which is highly polluting. It is also an important component of bleaching mixtures based on hydrogen peroxide, as they work together to neutralize metals, such as iron, copper, and manganese, which catalyze the decomposition of peroxide. It plays a fundamental role in ink removal, lifting it from the paper fibers and leaving it in suspension, thus preventing it from redepositing.
Typical applications
Functions of the silicate
Key benefits
Cellulose bleaching with hydrogen peroxide
Chemical reaction.
Reduces the use of peroxide. Produces whiter cellulose. Removes ink.
De-inking
Detergency.
Removes ink.
Raw water treatment
Flocculation.
Clears the manure.
Coating
Flocculation.
Retains dust and particles on the wires.
Headbox additive
Film formation.
Resistant to grease and moisture.
Adhesives for lamination and labeling
Adhesion.
Economical. Strong adhesive.
White water treatment
Flocculation.
Increases the floc size. Enhances the bleaching.
For materials like cardboard, sodium silicate is used to increase adhesiveness, as it spreads well and penetrates deep into the material, ensuring the formation of strong bonds that resist heat and water. It increases rigidity and significantly reduces production costs.
Typical applications
Functions of the silicate
Key benefits
Coiled tubing
Adhesion.
Increases rigidity. Economical.
Fiber cylinders
Adhesion.
Increases rigidity. Economical.
Used together with alum, ferric salts, and other coagulants, sodium silicate increases the speed of floc formation, as well as their size, density, and stability. It is an excellent cost-effective coagulant for water treatment, both industrial and potable. It activates at lower temperatures and also acts as a filter. It reduces the amount of lead, copper, and other heavy metals in drinking water. It inhibits corrosion, forming a microscopic film inside the pipes that prevents metals from leaching.
Typical applications
Functions of the silicate
Key benefits
Lead and copper control
Chemical reaction.
Reduces the toxicity levels of metals.
Raw water and wastewater treatment
Flocculation.
Increases the floc size and the speed formation.
Prevention of pipeline corrosion
Film formation.
The protective film inhibits the corrosive attack on the metal.
Stabilization of iron and manganese
Chemical reaction.
Improves taste. Eliminates the phenomenon of "red water".
Sodium silicate is essential for regulating the pressure of chemical-resistant mortars and refractory cements. Cements built with soluble silicate binders withstand higher temperatures and attacks from potential acidic agents. Silicate is used to modify the physical properties of hydraulic materials, such as Portland cement. In fact, by adding silicate to cement, permeability can be reduced by increasing the quantity of bonds that form. It can be applied on the surface to increase resistance to water, wear, oily, and acidic substances.
Typical applications
Functions of the silicate
Key benefits
Hardening cement
Chemical reaction, sealant.
Hardener.Acid resistant.
Acid-resistant cements
Binder
Ease of use.Economical.
Refractory cements
Binder.
Strong adhesive. Excellent refractoriness and acid resistance.
Thermal insulation
Adhesion, film formation.
Flame-resistant adhesive.
Soil Consolidation / Cementation
Gelling reaction.
Economical binder.
Silicate is used in various ways in the textile industry, for example in the bleaching process because it counteracts the metals that catalyze the decomposition of hydrogen peroxide, maintaining the pH at the optimal level. It is used to remove waxes, oily substances, and residues from cotton. Furthermore, it is used in cold dyeing processes because less water is needed, it operates at lower temperatures, and it better fixes the dye.
Typical applications
Functions of the silicate
Key benefits
Peroxide bleaching
Chemical reaction.
Reduces the use of peroxide. Further whitens the whites.
Cold pad batch dyeing
Buffering.
Fix the dye.Lowers processing costs.
In this context, it is used as a deflocculant in the processing of raw clay and other metal mixtures. It reduces the viscosity of the mixture, making it easier to add and process. This promotes the elimination of impurities and lowers production costs. The silicate also acts as a buffer for any alkalis present, further reducing processing costs.
Typical applications
Functions of the silicate
Key benefits
Refractory cements
Binder.
Pressure regulation.Breakage resistance.
Slip Casting
Deflocculant.
High concentration of solid components.
Sanding of the mixture
Deflocculant.
Reduces water.
Clay refining
Deflocculant.
Improves the fluidity.
In this field, the use of sodium silicate serves to increase the extraction yield, reacting with the fats present in the oil, emulsifying them. It counteracts excess shale and lowers processing costs. It prevents corrosion and is used in the preparation of drilling mud.
Typical applications
Functions of the silicate
Key benefits
Drilling mud
Chemical reaction.
Controls excess shale.
Prevention of corrosion
Chemical reaction.
Effective. Economical.
Emulsion rupture
Chemical reaction.
Helps the emulsion rupture.
Silicate is used in several mineral processing and mining systems to increase the amount of valuable minerals extracted, reducing unwanted contamination. The main use in this area is as a deflocculant, to crumble clay. It inhibits corrosion to grinding bodies. It promotes the formation of granules. It increases the strength of those formed and, in addition, increases flow characteristics and cohesive properties.
Typical applications
Functions of the silicate
Key benefits
Porous castings
Impregnation.
Seals the leaks. Fills the gaps.
Coating of welding bars
Binder.
Good binder and melting action.
Mineral enrichment
Deflocculant.
Coadjutates separation.Controls corrosion.
Foundry Moulds and “core binders”
Binder.
High resistance.Eliminates fumes.
Melting powders
Clumping.
Eliminates dust.Improves environmental conditions.
Granulation
Binder.
It promotes the formation of granules. It increases the strength of those formed.
Briquetting
Binder.
Enhances flow characteristics and cohesive properties.
CUSTOMIZED ADVICE
Indicate the specific area of use in the message and you will be contacted by one of our technicians to identify the best product for your needs.